The Plastic Packaging Tax: What do you need to know?
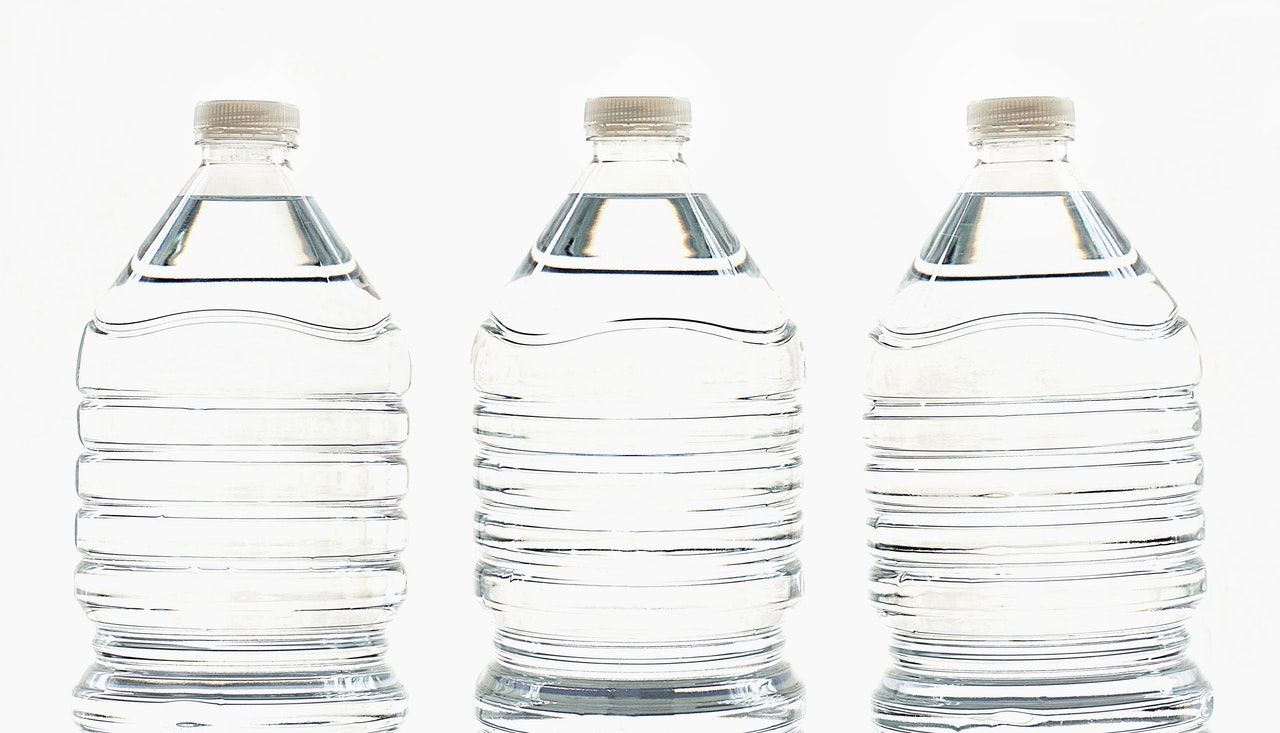
IFE Manufacturing speaks to Josh Remi, Commercial Manager at data specialist ecoveritas, to learn more about the introduction of the Plastic Packaging Tax and how it is impacting on businesses in the UK.
Briefly, what is the Plastic Packaging Tax and who does it affect?
The UK Plastic Packaging Tax (PPT) came into force on April 1 and applies to any UK business that manufactures or imports ten or more tonnes of plastic packaging per year. The tax is due on finished plastic packaging components that contain less than 30% recycled plastic and charged at a rate of £200 per tonne of packaging.
The environmental tax forms part of the UK Government’s bid to tackle avoidable plastic waste and aims to drive real and lasting change in the packaging industry.
The government estimates the use of recycled plastic in plastic packaging could increase by approximately 40% as a result of this tax.
Who is exempt from the tax, and do they need to take any action?
There are four categories of packaging exempt from the tax. They are products:
- used for the immediate packaging of licensed human medicine
- permanently recorded as set aside for non-packaging use
- used as transport packaging to import multiple goods safely into the UK
- used in aircraft, ship and rail goods stores
Exempt packaging which counts towards the 10-tonne threshold for registration
Plastic packaging used for human medicinal products, and plastic packaging permanently recorded as set aside for non-packaging use, must be included when working out the total weight of packaging manufactured or imported.
Exempt packaging which does not count towards the 10-tonne threshold for registration
Plastic packaging used for transporting imported goods, and for stores on international aircraft, ship and rail journeys, does not need to be included when working out the total weight of packaging manufactured or imported.
Packaging excluded from the tax
There are three types of products excluded from the tax. These do not need to be included when working out the total weight of packaging manufactured or imported.
They are products which are deigned to be:
- used in the long-term storage of goods
- an integral part of the goods
- reused for the presentation of goods
Exemptions and exclusions to the tax have been kept to a minimum to encourage greater use of recycled plastic and stimulate the recycled plastic supply chain
However, with no exemptions for materials that come into contact with food and cannot be recycled, some businesses have no choice but to pay the tax. Along with limited availability in cost and quantity of recycled PET, this remains a subject of much debate and means increased costs, which could be passed on.
It is also worth keeping in mind that plastic components at all stages of production, including containment, movement, handling, delivery and presentation, are all subject to the tax, which can complicate matters when calculating potential outlays.
What information should businesses be gathering for the tax?
The new tax calls for greater collaboration and transparency within the supply chain. The businesses that manage their data effectively will be able to maintain a clear audit trail and prove, without doubt, the authenticity of the materials used in their packaging.
The tax returns will require information concerning the weight of:
- Chargeable plastic components that the business has produced or imported
- Non-chargeable plastic components that the business has produced or imported
- Chargeable plastic components where the direct export condition is not met
- Chargeable plastic components produced or imported for which the direct export condition is met
- Plastic components which are exempt because they meet the required threshold of 30% recycled content
- Plastic components that are exempt through current PPT legislation
Once registered for the tax, you’re required to keep the records for at least six years following the end of each accounting period.
In summary, the records are:
- Weight details of each plastic packaging component
- Details of the weight of plastic packaging exported, if applicable
- Evidence of recycled content, including how you’ve worked out the percentage of recycled plastic, its source, and what product lines the content is used with
- Evidence of why an exemption applies (e.g. packaging for medicine used for human medical products).
Notably, you should keep records even if you are below the threshold because of a rolling 12-month time period, so you could subsequently hit the limit and be liable to keep records and pay tax.
What long-term actions would you recommend businesses take?
Assess the likely PPT impact on the business
Gain an understanding of how potential tax liabilities will affect the business, with a top-level view of existing packaging designs and any potential exemptions. This is not purely in terms of cost, but in allocation of resources.
Review your supply chain to determine what will be affected and who will be responsible
Identify who, within the business, will be taking ownership of PPT compliance. Some supply chains are naturally more complex, which means auditing and reporting may be extremely resource intensive.
Make any required amendments to contracts and pricing
Businesses looking to increase their recycled plastic content to ensure it is above the 30% threshold must have their new supply streams in place, particularly as the material becomes more scarce and tougher to acquire. In addition, it’s important to identify where the PPT costs will manifest, such as price increases for customers.
Engage with customers and suppliers
Clarity and communication are key – let customers and suppliers know if new PPT tax liabilities are likely to increase costs or if alternative options will be explored. Similarly, advise the supply chain if your packaging will be exempt from the tax.
Interrogate existing data collection and reporting
To know how prepared a business is for its new reporting obligations with regards to recycled plastic content, it’s important to understand what data is currently being collected, how, where it is stored and what it is used for.
Identify potential gaps in data collection
By auditing existing data collection, any gaps can be identified. As mentioned above the PPT returns will require complex information concerning your plastic components.
Implement required system changes
Following thorough analysis of current reporting capabilities, it may become apparent that system changes are required in terms of how data is collected and stored. In this case, it is prudent for businesses to action these changes well in advance and ensure there are no gaps once the plastic tax reporting obligations take effect.
Partner with a specialist
Businesses should look to partner with a packaging data specialist that can consistently deliver a highly efficient and transparent service without the need to scale up to meet the requirements. Ecoveritas offer global data collection and analysis services that can be combined with compliance, guidance and consultancy support. Our range of tools and expertise help businesses navigate the rules of the new legislation. With support, businesses can continue to operate compliantly, competitively and with complete confidence.
Apart from the most obvious element - the financial cost of the tax - businesses also have to consider the additional overheads in gathering evidence and reporting information. For instance, do businesses bring a specialist data handler in to handle new regulatory compliance or are the responsibilities given to existing team members? If it’s the latter approach, would this harm productivity and output? These questions are just a few examples of how the administrative burden brings several potential impacts to the supply chain.
What impact do you think the tax will have on UK businesses?
The costs, of course, have to be absorbed by the supply chain in some way but the short-term pain could lead to significant long-term gains.
The real litmus test will come at the end of July 22 when the first returns and payments are due. It’s easy to dismiss the tax as just another added cost placed on packaging providers but, in reality, the tax has good intentions and that shouldn’t go unrecognised.
If it is successful, it will help secure the long-term development of packaging and its end markets, alongside a potentially much stronger infrastructure for recycled plastic. However, there are a lot of hurdles to overcome – the procurement of recycled content in good quantity chief among them. If the tax works as intended, it could yield a lot of industry and environmental benefits over the longer term.
To keep up to date with the latest industry news and trends, subscribe to the IFE Manufacturing newsletter.